We decided to take a deep dive into skid plates and armor to check out some of the differences between Steel vs. Aluminum skid plates and how their properties and designs can protect your off-road vehicle. From Rock crawling to trail riding skid plates are designed to protect your vehicle and give you a piece of mind. We dive in and dig into all the gory details to provide you with some guidance on gearing up for your off-road mission.
Off Road Mission
If you’re like me and out researching choices for skid plates and armor for your vehicle, you have a mission in your mind that you’re looking to accomplish. For me, it’s all about towing my Rooftop tent on my trailer around the beautiful Southern Colorado Jeep Trails and experiencing the mountains firsthand.
In my case, I love off-roading in the San Juan mountains and excursions to other remote locations such as Moab or my nearby off-road playground Hidden Falls Adventure Park. Both of which have piles of rocks that will eat the underside of my Jeep if not careful.
For me, my mission isn’t that of hardcore rock crawling, but of more trail riding and back country driving. When out on these trails my experience suggests that one of the most common issues, I’d like to defend against is shear forces. I’ve noticed when out on the trails when I feel I’m bouncing around the most that lateral movement across a surface during acceleration/slippage or lousy line or sliding off a rock (or the rock sliding out from under me).
I also seek out something that is tough and durable – so to achieve these goals I started to research the materials science quantification of what is considered sturdy and durable.
Beyond protecting your vehicle, it’s important that any time you’re out off-roading that you pack along these off-road essentials. Skid plates and body armor are there to increase protection against damaging parts of your undercarriage and vehicle, but they won’t protect you from flat tires, road hazards, breakdowns, and other issues.
Skid Plate Engineering
When it comes to these materials, the engineering choices are what should drive your gear selection. When we did our research, we found steel skid plate armor is often 3/16″ and aluminum is 1/4″ thick. In some measurements,
This thickness gives the materials a “Same Standard” in that for some use cases the desired result is nearly the same.
I’ve reached out to a few manufacturers and vendors to ask some questions on their engineering design decisions, but until I get a response, I did some research on describing the material science differences of the two materials used in Skid plates.
I’ve broken down many of the property’s engineers used in developing armor solutions and have tried to show how they relate to skid plates.
Disclaimer: I’m not a materials science or certified engineer – This post is the result of research on the topic of aluminum vs. steel skid plates. Please let me know if you find any issues with our descriptions or math, and we’ll update the article as needed. (Register to comment below!)
Engineered properties
Geometric Stiffness – the geometry of the shape and how it impacts stiffness – will the part bend?
Structural efficiency – the mass a structure can hold divided by the mass of the structure.
Hardness – the relative resistance that its surface imposes against the penetration of a harder body
Strength – the amount of force a material can withstand and still recover to its original shape
Toughness – the amount of energy that a material can absorb before fracture.
Stiffness – A mechanical property of linear elastic solid materials.
Deflection – Beam or load condition of a material with a fixed end.
Geometric Stiffness of skid plates
Without having the engineering diagrams and formulas for each type of skid plate to calculate against, I can only speak to this as a general reference that benefits both aluminum and steel plates.
The geometry of the plates needs to have a design so that the strength, toughness, geometric stiffness, and structural efficiency are distributed not only amongst the armor but through the vehicle.
The geometric stiffness of the product should be designed equally into each product whether its steel or aluminum. Both will fail with improper geometric properties (and installation).
Steel has a slight benefit when it comes to parts that need to be thinner as the stiffness and strength will be higher than aluminum.
Structural Efficiency
With regards to structural efficiency – the ratio of a material’s stiffness to its density, aluminum is shown to have a structural efficiency much greater than steel. An aluminum plate of equal thickness will weigh 57% the equivalent steel plate and designed to the same stiffness; an aluminum plate will weigh ~ 45% of the same steel plate.
If you’re resting on an object and the mass of your vehicle is resting on your skid plate, then the structural efficiency by weight scales in the factor of aluminum but thickness it scales in favor of steel.
Hardness of skid plates
One way to measure the hardness of the material is the materials “Mohs scale.” The Mohs scale represents the resistance the surface imposes against the penetration of a harder body. Hardness is an excellent quality to have for something such as a skid plate for your fuel tank since your goal should be to resist puncture and have fuel to get home safely.
Mohs scale of hardness:
The Mohs scale of mineral hardness is a qualitative ordinal scale that characterizes the scratch resistance of various minerals through the ability of a harder material to scratch a softer material
- Aluminum Hardness = 2-3
- Steel Hardness = 4 to 8
As you can see the hardness of steel is twice the hardness of aluminum at equal thicknesses. The measured proportional hardness is one area where aluminum plates are engineered to be thicker than steel.
When it comes to hardness, steel at the same thickness is the harder material but aluminum being lighter can be made thicker and have a better weight benefit. The choice is here a ton of protection at a higher weight or some protection at a lower weight. If you’re mostly scratching your JKU tank because of the longer wheelbase, then Aluminum affords enough protection, but if you’re dragging across rocks in extreme rock crawling, I will go with steel.
Strength of Skid Plates
What would be some characteristic properties of engineering skid plates? For protecting a fuel tank, you may be interested in shear strength and impact strength and the yield strength of the material.
Shear strength: Think of shear strength as the ability of the material to withstand being cut across like scissors, the stronger the shear strength the harder it is to shear the materials in its cross sections.
Impact Strength: This is the amount of energy absorbed before fracture.
Yield Strength: The yield strength of a material is the point at which a material begins to deform plastically. Before failing in such a way said material would return to its original shape when the applied stress is removed.
Once the yield strength is surpassed some fraction of the deformation will be permanent and non-reversible.
Shear Strength
Shear strength is the strength of a material or component against the type of failure where the material fails in a shear. In structural engineering, the shear strength component is important for designing the dimensions and geometry of the materials used.
- Steels – 0.75 UTS (Ultimate Strength Relationship) and .58 TYS (Yield Strength Relationship)
- Aluminum – .65 UTS and .55 TYS
UTS is the maximum stress above which the material will break
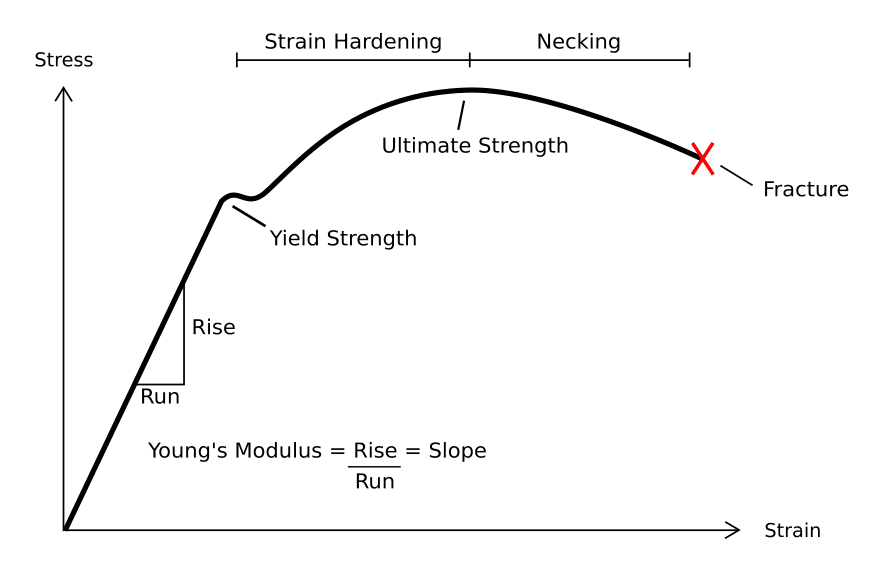
TYS is the stress at which a material deforms permanently. In the case of Aluminum vs. Steel skid plates, the shear strength of the materials and geometry of the equipment are the primary design difference. The materials are equal in relational UTS and TYS when you figure in the thinner steel vs. thicker aluminum and geometry of the design.
Impact Strength
In general, for a given volume of material, steel will absorb more energy than aluminum. For a given volume, aluminum weighs only 1/3 as much as steel. If you could afford 2/3 more aluminum (thickness), then you could exceed or meet the impact strength of steel. However, this isn’t optimal for clearance of off-road vehicles.
Yield Strength
- aluminum yield strength: 35mpa (megapascal) – 5076.3195 PSI
- steel yield strength: 205mpa = 29732.7285 PSI
Steel has six times the yield strength of Aluminum. In this case, the geometry and thickness of aluminum would have to play a greater role to protect your vehicle in the case of yield strength tensions.
Stiffness
In simple terms, a stiff material needs more force to deform than a soft material. Youngs modulus is the measurement of a material’s stiffness.
Youngs Modulus:
- Steel 205 GPa
- Aluminum 70 GPa
The Shear modulus represents a material’s rigidity.
The shear modulus of 1018 steel vs. AA 2024 – Carbon Alloy vs. Aluminum Alloy
- Steel: 11603 ksi
- Aluminum 4029 ksi
A material having a large shear modulus is difficult to bend. Differences in shear modulus can be alleviated by the geometric properties of the skid plate as well through better supports, transfer of stress and strain or even by a designed failure of the part.
Toughness of skid plates
When it comes to resisting fracture, steel has a higher tolerance as seen in the graph below. Aluminum can be made thicker to increase the toughness but must be exponentially thicker to achieve parallel toughness. On an off-road vehicle, you wouldn’t necessarily want to trade off thickness for toughness since often clearance of your vehicle over obstacles is superior to skidding over obstacles, to begin with. If you already have great clearance and fracture isn’t a concern, then this property may not be part of your mission. I would also add that some people choose to accept fracture as a means of protection in that the skid plate failing is doing its job vs. having your vehicle disabled. Now if you do something that impacts both your plate and vehicle, then steel would offer the best protection.
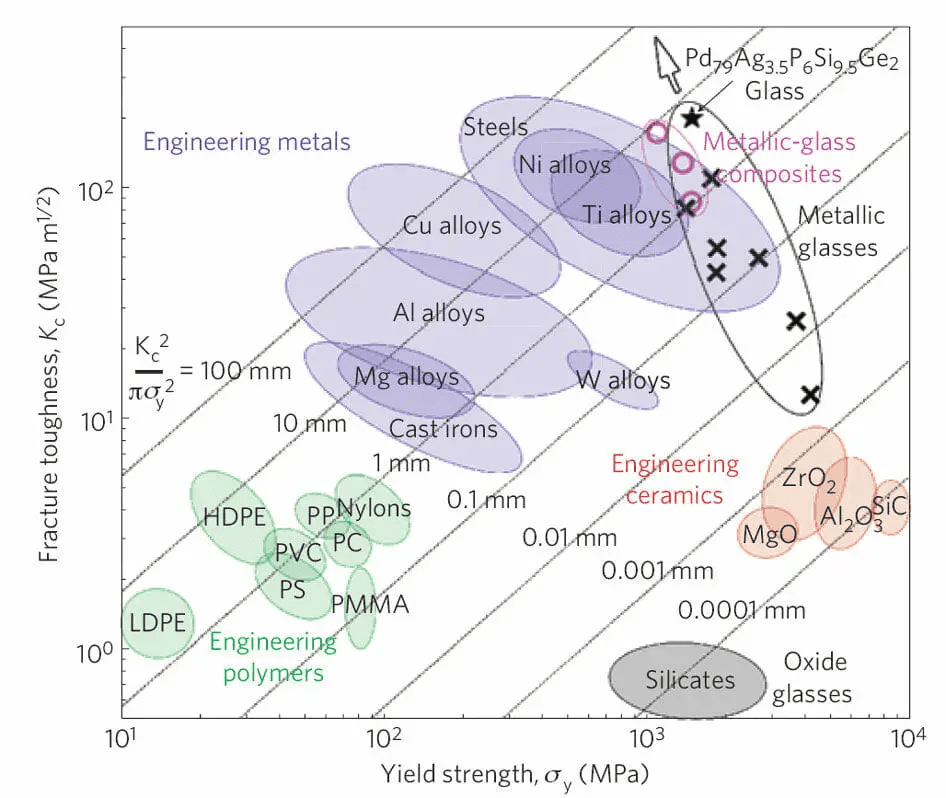
Skid Plates – Deflection
One formula to understand the engineering of aluminum vs. Steel is the beam deflection calculator. This treats the stress as if the item is a diving board, stress at the end of an item. This isn’t much of an issue in most installations, but I have seen armor for drive shafts and axles that may fit this paradigm.
To keep the math easier this was calculated on a 20″ by 20″ by .25 (1/4) inch piece of aluminum vs. the standard size of 20″ by 20″ by 3/16″ (.1875″) for Steel on a 4000 lb load. (Calculated on Wolfram Alpha)
Aluminum deflection:
- Deflection (inches) – 40.96
Bending Stress (psi) – 384000 - Energy (joules 9255.62
Steel deflection:
- Deflection (inches) – 32.36
Bending Stress (psi) – 682666
Energy (joules) – 7313.0notes:
If deflection is a concern – such as armor that doesn’t connect at both ends but has a support structure that extends out then steel is by far the best and only choice.
Aluminum vs. Steel skid plate Costs
In comparing products from the same vendor (to remove variables of brand cost differences), aluminum skid plates have a higher overall cost than steel skid plates.
According to fueleconomy.gov, 100 lbs. weight can make your car 1% less efficient when it comes to gas mileage. On a Jeep which is already a brick driving against the wind most of the time, this number is slightly larger. Let’s say adding aluminum skid plates saves you 50lbs over steel skid plates and you plan to drive your vehicle for 150k miles. Saving .02cents/gallon
Using EPA averages (which are hard to meet) let’s say you get 18MPG.
150,000 / 18 = 8,333 gallons of gas over lifetime * .02 (fuel economy cost of weight) = $167 dollars in gas savings
Over the life of the car, the 50lbs may not add up to much since the cost of aluminum surpasses steel by as much as the total savings. However, if you do the above math on a more reasonable and real ~15mpg efficiency of Jeeps, it will slightly favor aluminum even more. (Especially if fuel prices go up)
Feedback Request: If you have a newer JLU with the turbo or diesel, I would love to hear about your mileage and experience with skid plates and added weight. Leave a comment below!
Where weight may have a bigger cost saving is in affording you weight in other areas such as bumpers/gear or reducing stress on components such as lift and shocks preserving lift heights and such.
Aluminum vs. Steel skid plate Corrosion & Fatigue
Aluminum is subject to fatigue failure (its endurance limit) wherein steel fatigue is not normally an issue with the exception that both have limits around engines. (vibration). One would normally mitigate this by providing cross support and bracing/connections to reduce deflection & fatigue.
An advantage of aluminum is that aluminum will not rust and doesn’t need a touch-up painting, however, it will corrode, but such corrosion creates an oxide barrier which prevents further corrosion. If you don’t touch up paint on scratched steel, the steel may rust and corrode leading towards premature failure.
Buy Online
- FITMENT | Fits 2018-2023 Jeep Wrangler JL 4 Door
- Modular skid plate system with Trail Armor Technology delivers axle-to-axle coverage for rugged underbody protection
- Dual-layer construction features ¼-inch thick aluminum plate with impact-resistant, easily replaceable, and easy-to-clean UHMW armor-coated panels
- Fully modular design supports individual skid plate removal for painless vehicle maintenance
- Installs utilizing factory mounting locations with included flush-mount hardware
- 5052 ALUMINUM CONSTRUCTION – Our high quality skids are made from stamped 5052 aluminum, providing lightweight and strong underbody protection. The…
- STRONG UNDERBODY PROTECTION – The 6mm thick aluminum panels are the next evolution in under body protection, providing superior strength and…
- PRECISION FIT – Protect your Fuel Tank on your JK with this Quadratec Aluminum Modular Fuel Tank Skid Plate. Each panel is laser cut and press formed…
- DENT RESISTANT – Aluminum’s density is about 1/3 that of steel and the advantage of the increased material thickness to offset strength actually…
- SIMPLE INSTALLATION – This Modular Skid Plates are a simple no drill installation that’s easy to install with the included hardware and brackets….
- Made from durable 1/4″ plate steel
- Protects your rear diff from off-road hazards
- Corrosion-resistant black powder coat
- Easy bolt-on installation
- Backed by Rough Country’s Lifetime
- Easy At Home Bolt On Installation
- Protects your gas tank from off-road hazards
- Estimated Install Time: 1-3 hours
- Includes – Gas tank skid plate, Mounting brackets, Hardware
- Backed by Rough Country’s Lifetime Warranty
Affiliate links & Product Images are from Amazon Product Advertising API.
Make sure that as you shop for skid plates that you shop for your appropriate year, model, and make of vehicle. They will vary between 2door, 4 door and CJ, YJ, JK, JL Jeeps.
Aluminum vs. Steel skid plate Wrap Up
All said and done; I believe aluminum skid plates will work for my mission to help provide protection for critical components on my Jeep to reduce the possibility of being disabled while out on remote mountain trails. If your mission is hardcore rock crawling you expect to drag/slide and bounce your vehicle over rocks, then steel plates may still be your best option. The reduced weight of aluminum, the shear strength and improved hardness and toughness over not having anything to me is better than having nothing and optimal for my mission in weight savings and ease of maintenance.
I’m personally excited to see expansion into aluminum and hope material sciences will continue to improve to reduce weight, improve the efficiency and safety of vehicles. I’m not entirely sure it’s worth the extra cost vs. steel, but I will say an engineered aluminum solution does offer protection and an overall weight saving and with a lower weight, ease of install is a wonderful thing too.
In the end though, it’s a tough call and more of a personal choice. In some respects, the steel wins hands down when it comes to overall engineering properties on paper, but, it may be better to have a skid plate fail in some cases rather than have that potential energy transfer to the vehicle.
For example, it may be better to shear off a part of your skid plate at extreme stresses with an aluminum plate than it would be to absorb said forces on a steel plate and potentially break off bolts/connections/rods. In other words, the failure of the skid plate may be the skid plate doing its job.
Again, I’m not a trained engineer. I would love some feedback so please post your experiences and thoughts in the comment section below. Registration is quick & easy. I’ll also try and update this post with more direct links to Wolfram for the actual math for those who want to experiment around.
Safe Trails!
Great evaluation between the Aluminum and Steel. I have been doing similar research but don’t understand why the mfr’s don’t run testing on the two products. I don’t want to add to large of a lift and upset the factory settings on my 2017 Rubicon so keeping it as light as possible really makes a difference. In the end, I haven’t made a decision between the two, and I might just do a combination of both. Steel to the areas that receive the most impact (after a few more trips out I should have that figured out) and aluminum where little to no impact occurs.
Thanks for the feedback! I’m in the same boat, I’m not as interested in massive changes to my vehicles geometry and I don’t really want to absolutely kill my fuel efficiency either. I think going aluminum for some protection and steel for other pieces is a good mix. I’ll plan on updating this post as I add pieces to my vehicle and gain experience.
I like that you pointed out that although aluminum plates may be thicker, they still weigh less than steel, which can help give your a weight benefit. I also like that they area less expensive. My uncle lives in the country, so he’s been wondering which type of metal plates would best fit his needs. I’ll share this article with him, so he can make an informed decision.
Over the years I like to think of Aluminum skid plates as preventative protection for ensuring vehicle safety/protection when you’re out and about – mostly overland and trail driving. I’d recommend heavy duty steel if your intention is purposefully rock crawling and knowingly driving in areas where you intentionally “slide”.
Hi –
What grade Al would you expect would be good for skid plates?
2024?